Five Major Process Choices For Sportswear Manufacturing
Abstract
In the field of sportswear manufacturing, the choice of sewing process directly affects the functionality, comfort and market competitiveness of the product. Traditional sewing methods (such as flat seams and three-thread lock seams) often cannot meet the needs of high-intensity sports due to problems such as seam friction and insufficient elasticity.
This white paper systematically analyzes the five most mainstream sewing processes in sportswear production, focusing on the technical advantages and commercial value of **Flatlock Seam**, and provides scientific selection basis for brands and buyers.
Ultra-high elasticity: lateral stretch rate ≥80%, far exceeding ordinary flat seams (≤30%), suitable for large movements such as yoga and running.
Zero friction experience: the seams are flat and smooth to avoid skin abrasions (Lululemon Align series standard process).
Extreme durability: Martindale test seam slippage <2mm, still firm after 50 washes.
2. Heat Seal Bonding
Process principle
Use TPU film to press the fabric seams at high temperature, completely without needle and thread marks.
Advantages and limitations
✅ Advantages: Absolutely traceless, suitable for sensitive areas (such as sports bra cup joints).
❌ Limitations: The cost is 40% higher than four-needle six-thread, and it is only applicable to chemical fiber fabrics (cotton/linen is not available).
3. Ultrasonic Welding
Process Principle
High-frequency vibration fuses the fibers, without needles, threads, or glue.
Advantages and Limitations
✅ Advantages: Environmentally friendly and pollution-free, excellent waterproofness (commonly used in outdoor jackets).
❌ Limitations: Poor elasticity (stretching rate <15%), only for synthetic fibers.
4. 3D Seamless Knitting
Process Principle
Fully computerized knitting machines directly weave garments, completely seamless (such as Adidas Primeknit technology).
Advantages and Limitations
✅ Advantages: Peak comfort, close to zero material waste.
❌ Limitations: High equipment cost (more than $2 million per unit), long delivery cycle.
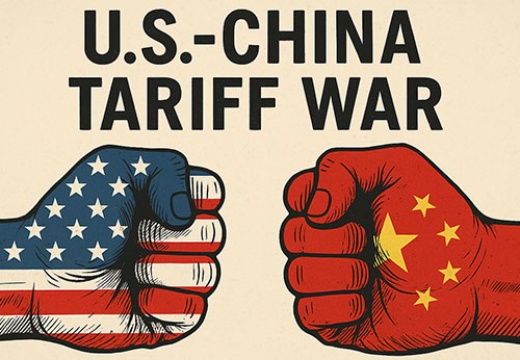
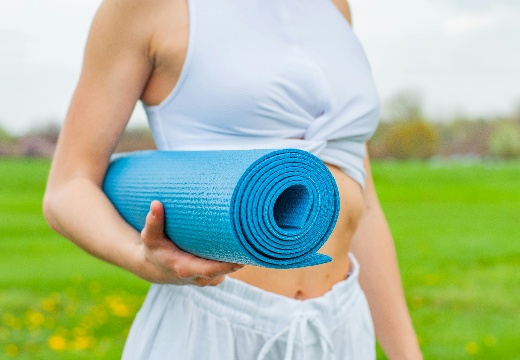
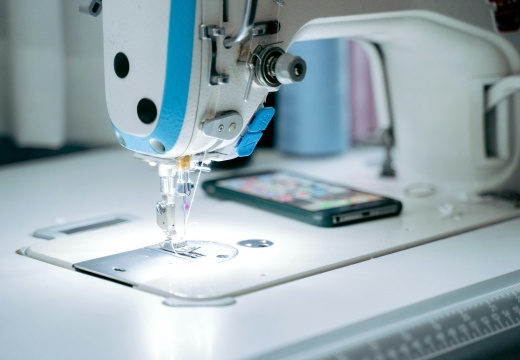